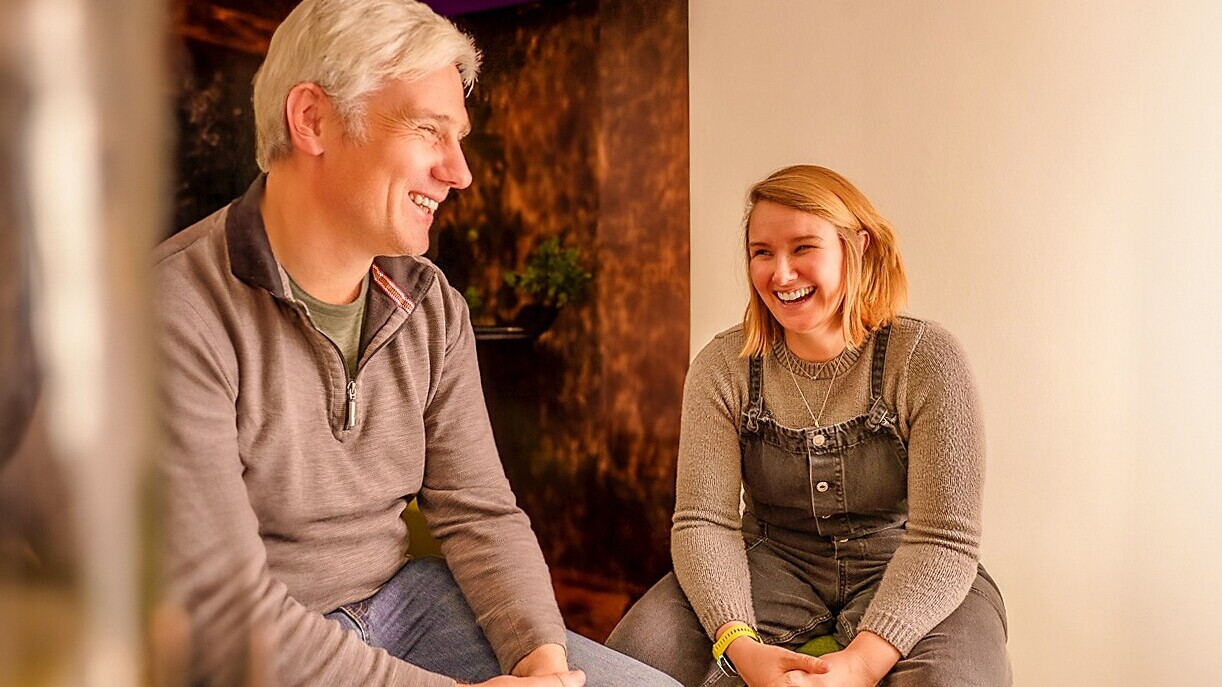
UK and Luxembourg-based startup Uplift360 has landed €1mn in pre-seed funding to scale up a greener method for recycling advanced materials like Kevlar.
Uplift360’s patent-pending process breaks down Kevlar and other composites without compromising the integrity of the fibres and resins. These raw materials can then be reused to make new products. It does this using safe chemicals and at room temperature — making it greener and more energy-efficient than traditional methods, the startup claims.
“It’s a game-changer,” Sam Staincliffe, Uplift360’s co-founder and CTO, told TNW in an interview. “It means we can lower costs and recycle a wide range of advanced materials without the harmful impacts.” The process can also break down carbon fibre and glass fibre.
Uplift360 will use the fresh funding to accelerate R&D, mature its technology and expand its team of scientists and engineers. Over the next 12 months, the company will set up its first concept demonstrator plant at its lab in Luxembourg, as it looks to woo potential customers, including DuPont: the American chemical conglomerate that first invented Kevlar.
Giving body armour a second life
Staincliffe, a defence tech expert, founded Uplift360 alongside Royal Airforce (RAF) veteran Jamie Meighan in 2021. Their mission was to help green the defence sector, which by one estimate contributes 5.5% of global greenhouse gas emissions — more than Russia.
First, the founders considered recycling military uniforms until Dr Debra Carr, a textile scientist working for the UK’s Defence and Security Accelerator (DASA), suggested they look into body armour. More specifically, para-aramid fibres — aka Kevlar.
DuPont chemist Stephanie Kwolek invented Kevlar in 1965. The material, which is five times stronger than steel, is best known for stopping bullets, but it’s also found in planes, cars, boats and many other products.
Today, Kevlar vests are incinerated after around 5 years of use. They are never recycled. That’s partly because traditional recycling methods aren’t up to the task. Governments also don’t want body armour ending up in the wrong hands.
Either way, it’s a big sustainability problem. It can take over 37 kilograms of petrochemicals to make one kilogram of Kevlar, so making new ones all the time isn’t exactly good for the planet.
Burning Kevlar also doesn’t make economic sense. Para-aramid fibres cost 85 times as much per weight as steel. A single vest can cost up to €3000. This makes Kevlar “waste” pretty darn valuable.
‘Matter of national security’
Last year, Uplift360 secured €600K in funding from the UK’s Defence and Security Accelerator (DASA), as the country’s Ministry of Defence looks for innovative ways to green its supply chain. It also wants to cut reliance on foreign powers for key materials.
“The defence industry in the UK and Europe has a pretty fragile supply chain,” said Staincliffe. “Recycling and reusing isn’t just about sustainability, it’s also a matter of national security.”
However, the startup’s first customers will likely not be the users of products like Kevlar, but the manufacturers of them. Uplift360 is already trialling its technology with DuPont and Teijin, a Japanese company specialising in high-performance fibres.
The aim is to build recycling facilities at these firms’ factories. The plants will take in old products and recycle them for reuse to make new ones.
While Uplift360 is focusing on Kevlar recycling for now, the company plans to put its chemicals to work on a range of tough stuff in the future — from aircraft components to wind turbine blades.
Get the TNW newsletter
Get the most important tech news in your inbox each week.