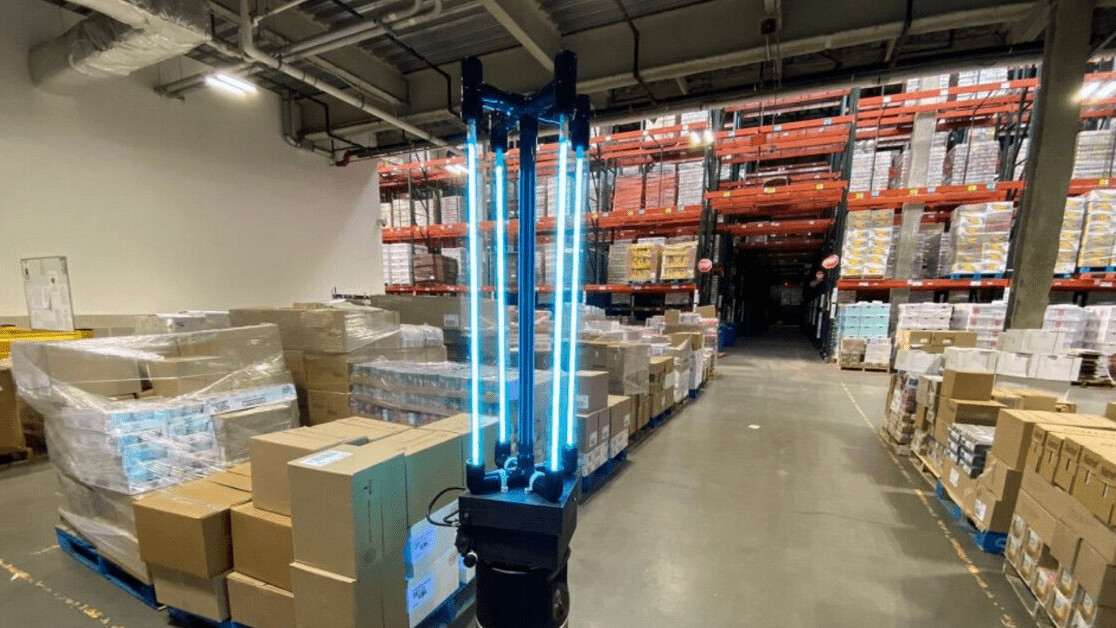
A new MIT robot that uses UV light to kill the coronavirus could be used to disinfect warehouses, schools, and offices.
The system has already been used to sanitize the Greater Boston Food Bank. In tests, the robot covered a 4,000 square foot area of the warehouse within 30 minutes, providing enough light to neutralize around 90% of coronavirus particles.
Scientists from MIT’s Computer Science and Artificial Intelligence Lab (CSAIL) designed the light-emitting vertical bars that shine UV light onto surfaces. They then attached the fixture to a mobile robotic base produced by Ava Robotics.
You can check it out in action in the video below:
The researchers believe the system could be used in an array of different venues, such as factories, restaurants, and supermarkets. But first, they need to enhance its autonomy.
Increasing autonomy
The system uses a short-wavelength of ultraviolet light, known as UV-C, to break apart germ DNA. Studies show that UV-C can kill other coronaviruses, such as SARS, and it’s already widely used to eradicate COVID-19 in China. However, it can also damage skin and eye cells, so humans need to wait outside while the lights pump out their ghostly blue beams.
Currently, teleoperators must first teach the robot a route around the site. It then follows waypoints around a map of the venue, which show the droid where to go and point the light.
The next step is enabling the robot to adapt to changes in its environment. In the food bank, the position of pallets varies every day as staff move them to different aisles in the warehouse.
“We’ve started to identify known static components of the map,” CSAIL research scientist Alyssa Pierson told TNW. “These are things that never change, such as the walls in the environment as well as large metal shelving for the pallets.
“We’re also looking at defining zones where things change so there may be obstacles there, which allows the robot to focus on where its attention should be.”
[Read: How an AI learned to stitch up patients by studying surgical videos]
The system currently uses a 3D camera to navigate around obstacles and 2D LiDARS to measure distances by illuminating targets with light. Pearson says this is sufficient for warehouses, but that further sensors may be required for other locations.
But for now, her team is focused on food banks, which have faced a huge rise in demand since the pandemic began. Protecting their staff from infection will help them support the millions of people pushed into food insecurity.
Get the TNW newsletter
Get the most important tech news in your inbox each week.