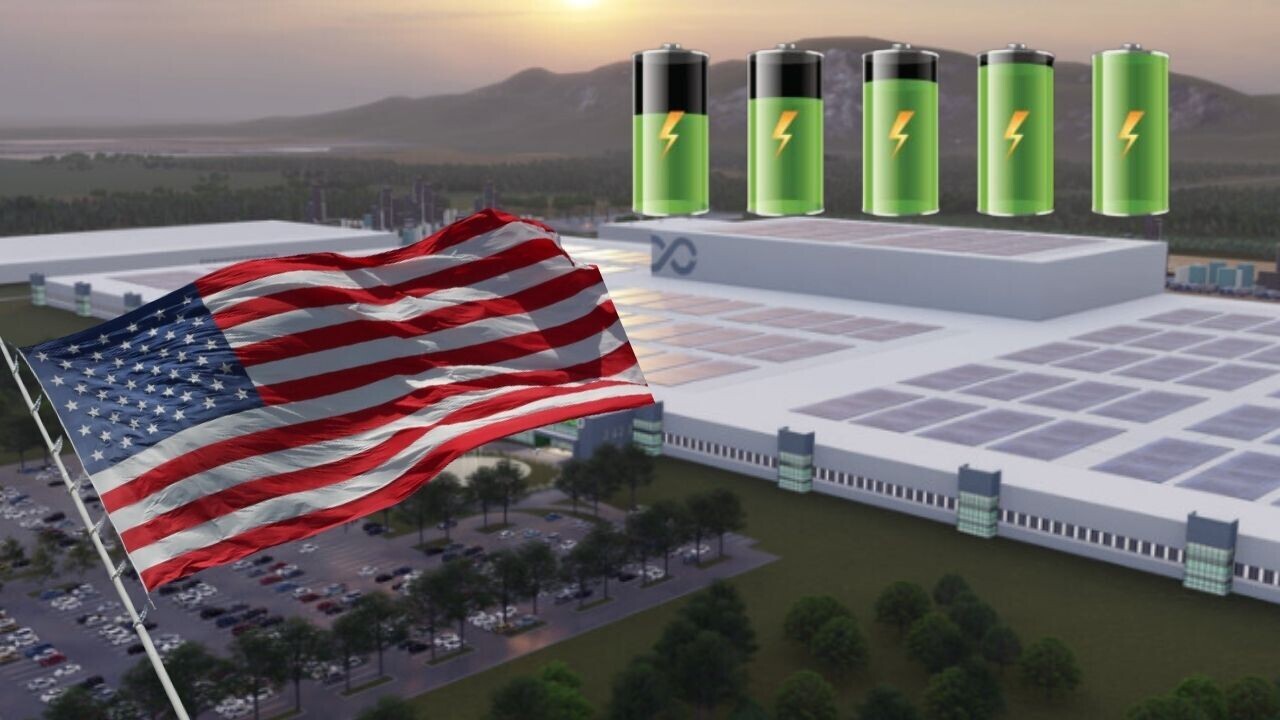
Did you know SHIFT is taking the stage this fall? Together with an amazing line-up of experts, we will explore the future of mobility during TNW Conference 2021. Secure your ticket now!
Even though the transition to battery electric vehicles is at an early stage, we’re well aware of the need to recycle and reuse the precious metals and materials contained within lithium-ion batteries.
Among the US recycling companies, Redwood Materials has emerged as a very competitive player, since its founding in 2017 by J.B. Straubel. Interestingly, Straubel revealed to Bloomberg that his company’s aim goes beyond recycling to bringing the battery supply chain from Asia to the US.
Filling the gap
Before Redwood, most US recycling companies simply ground up the batteries into a crude powder known as “black mass” for easy transportation. Then, they shipped those materials overseas to be refined and processed, according to Jeffrey Spangenberger, director of the Department of Energy’s ReCell Center.
However, this process has two disadvantages: the environmental impact of the materials’ transportation, and the dependence on foreign suppliers.
“We want to buy these materials once and then keep them here,” Spangenberger said. “The recycler and the manufacturer together — if that can be done under one roof, then we’re answering two questions at once.”
Redwood’s triple aim
The company wants to do away with the 80,000 kilometer (50,000 miles) supply chain of battery components, which are needed for the final production of an EV battery in the US.
For this reason, Redwood is seeking three types of operation: recycling, manufacturing copper foils for anodes, and producing cathodes.
Recycling is already taking place at the factory in Carson City, Nevada, where the company has its headquarters.
Redwood has also starting working on a second factory in Nevada to manufacture the delicate copper foils of anodes (the negative terminal of the battery), which are in short supply.
However, the production of cathodes (the positive terminal of the battery) is by far the most significant addition.
Why domestic production of cleaner cathodes is important
First, the cathode is the most expensive part of the battery. Some 10% to 30% of a cathode is made from cobalt, priced at approximately $28,500 per ton. This makes cobalt the priciest element of a cathode, more expensive than nickel, manganese, and aluminum combined.

Secondly, the cathode is also the most pollutant part of the battery. The mining of the raw materials that comprise it, their virgin refinement, and their transportation overseas not only increase production costs dramatically, but also increase greenhouse emissions.
Redwood’s plan for consolidating the cathodes’ supply chain in the US
Straubel is searching for a new location in Nevada to build a new million-square-foot factory. He explains that the plant will produce enough cathode material for 100 gigawatt hours of batteries a year by the end of 2025.
This translates to about 1.3 million long-range vehicles annually, which matches the capacity of the biggest producers in Asia.
The company’s big target means that it can’t solely rely on recycled elements. Its aim, therefore, is to use 50% recycled and 50% raw materials.
Currently, EV batteries account for less than 10% of Redwood’s recycling stock, but the retired batteries from consumer electronics are abundant.
The real value of recycling and domestic production
Nevertheless, even with 50% of recyclable materials, the consolidation of the supply chain in the US would have a tremendously positive environmental impact. According to BloombergNEF’s analyst James Firth, it would reduce the emissions from battery-pack manufacturing by at least 41%.
Straubel believes that in the next decades recycled materials will be used for almost 100% of the world’s battery production. And if he’s right, not only would batteries become more affordable, but also make their production — which still raises concerns — significantly greener.
Do EVs excite your electrons? Do ebikes get your wheels spinning? Do self-driving cars get you all charged up?
Then you need the weekly SHIFT newsletter in your life. Click here to sign up.
Get the TNW newsletter
Get the most important tech news in your inbox each week.