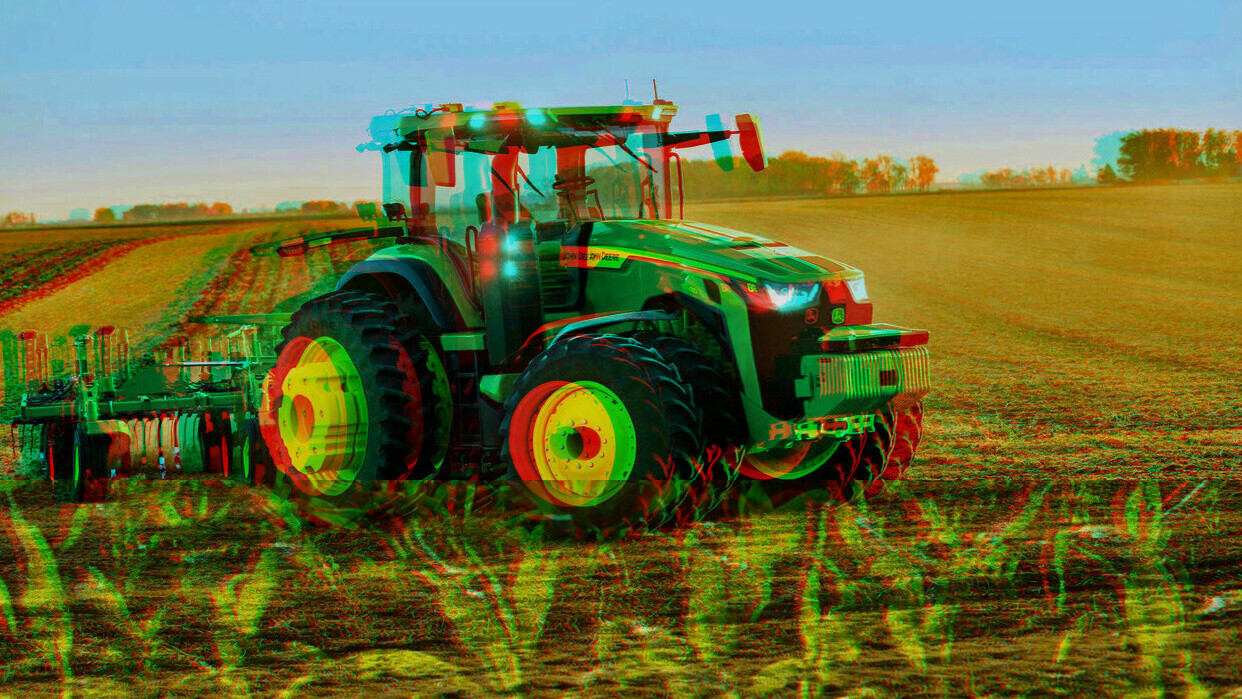
When you think CES, you might be picturing cool gadgets, smart home appliances, and fancy cars (well, if there are any that haven’t pulled out). And you’d be right. Kinda. Because one of the most exciting things on offer is John Deere’s very first autonomous tractor.
You read that right. An autonomous tractor. This is a version of Deere’s 8R vehicle and includes a TruSet™-enabled chisel plow, GPS guidance system, and far, far more.

Why do we need an autonomous tractor?
Farming labor shortages are a global problem as people migrate to cities. According to John Deere, the average farmer is over 55 and puts in 12–18 hours of work a day.

The autonomous tractor can run 24/7, although it needs refueling every 8-10 hours. Six pairs of stereo cameras enable 360-degree obstacle detection and calculate distance.
The autonomous tractor is also continuously checking its position relative to a geofence, ensuring it is operating where it is supposed to and is accurate to within less than 2.5cm (inch). This enables precise seed and nutrient spreading and harvesting without touching a steering wheel.
Machine learning and image recognition provide valuable precision data
According to Willy Pell, Vice President of Autonomy and New Ventures, the autonomous 8R tractor collected over 50 million images during in-field testing over the past three years. Each model is trained with hundreds of thousands of images, and its neural network classifies each pixel in about 100 milliseconds, and object detection determines if the machine moves or stops.

Pell explained that a lack of anomaly data had been a problem for the team:
It’s challenging to see events for which we have no training data. For example, if a billboard falls in a field. In response, John Deere built an anomaly detection system that recognizes anomalous systems, and when it encounters new objects, the machine just stops.
However, the anomaly detection appears to be a bigger sticking point than the company has admitted in their media launch event, telling The Verge that the function is far from autonomous. Instead, anomalous images are sent to “tele-operators” — essentially a call center of third-party contractors to manually determine if detected field obstacles are false positives or have been resolved. The farmer is then alerted of real issues via the app and tasked to decide upon a course of action.
The tractor can prepare over 325 acres of soil in 24 hours. It’s ready for large-scale production and will be available to farmers later this year.
Get the TNW newsletter
Get the most important tech news in your inbox each week.